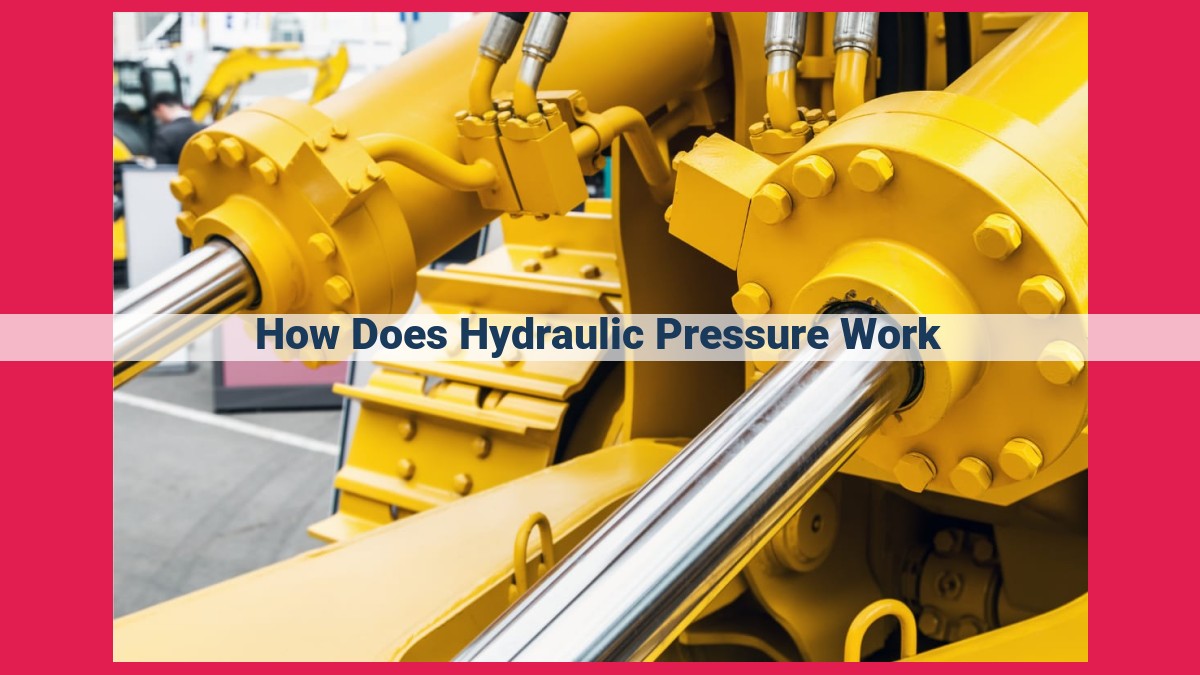
Unlocking The Power Of Hydraulic Pressure: An In-Depth Guide
Hydraulic pressure works by utilizing Pascal's Law, which states that pressure applied to a fluid is transmitted evenly throughout. Hydraulic pressure, measured as the force applied per unit area, is generated and transmitted through a hydraulic fluid. This pressure is directed to a hydraulic cylinder, where it converts into mechanical force. The components of a hydraulic system include the cylinder, fluid, pipes, and hoses, each playing a role in transmitting pressure, controlling flow rate, and ensuring efficient operation. Hydraulic pressure finds applications in industries like industrial machinery, construction equipment, automotive systems, and aerospace systems, enabling the efficient use of force and power in various applications.
Pascal's Law: Explain how pressure applied to a fluid is transmitted evenly throughout.
The Secrets of Hydraulic Pressure: Unleashing the Power of Fluids
Imagine a world where liquids are not just for quenching thirst, but possess the strength to lift heavy weights and control powerful machines. This is the realm of hydraulic pressure, a fascinating concept that has transformed industries from construction to aerospace.
Pascal's Law: The Equalizing Force
At the heart of hydraulic pressure lies Pascal's Law, a fundamental principle that governs the behavior of fluids. This law states that when pressure is applied to a point in a confined fluid, it is transmitted equally throughout the entire fluid. It's like throwing a pebble into a pond: the force spreads out in all directions, affecting every molecule in the liquid.
This remarkable property of fluids allows hydraulic systems to generate enormous forces by applying relatively small amounts of pressure. Imagine a piston pushing down on a column of fluid. The pressure created at the piston is transmitted evenly to every other part of the fluid, including the piston at the other end. This means that the force applied to the first piston is amplified and can be used to move heavy
In essence, hydraulic pressure serves as a force multiplier, enabling us to harness the power of fluids to perform tasks that would otherwise require much greater effort. From construction equipment that effortlessly lifts tons of weight to aircraft systems that control critical flight operations, the applications of hydraulic pressure are as vast as they are impressive.
Stay tuned for our next installment, where we'll delve into the essential components of hydraulic systems and explore how they work together to create this extraordinary force.
Hydraulic Pressure: The Science Behind Applying Force
In the realm of engineering and industry, hydraulics reigns supreme as a powerful force multiplier. At its core lies the concept of hydraulic pressure, the foundational principle that governs the transfer of force through fluids. Imagine an endless ocean of tiny particles flowing within a sealed system. These particles, when subjected to pressure, act as a fluid medium, transmitting the force in all directions with remarkable uniformity.
This phenomenon is elegantly described by Pascal's Law, a cornerstone of hydraulics: pressure applied to a fluid at any point is transmitted equally throughout the fluid. In other words, the hydraulic pressure experienced at every point is identical, regardless of the fluid's volume or shape. It's as if the force is spread out like butter on a toast, ensuring equal distribution.
Now, let's delve deeper into the quantitative side of hydraulic pressure. It is the ratio of the force applied to a fluid to the surface area over which the force is distributed. In the realm of hydraulics, this translates to:
Hydraulic Pressure = Applied Force / Surface Area
Imagine a hydraulic cylinder filled with fluid. When a force is applied to the fluid, it exerts an equal and opposite force on the inside walls of the cylinder. The surface area of these walls determines the magnitude of the resulting pressure. A smaller surface area concentrates the force, amplifying its impact, while a larger surface area disperses the force, reducing its intensity.
This principle forms the basis of hydraulic systems, where relatively small applied forces acting on a fluid can generate tremendous forces on larger surfaces. This is why hydraulics finds applications in a wide range of industries, from heavy machinery and construction equipment to sophisticated aerospace systems.
Hydraulic Cylinder: The Powerhouse of Hydraulic Systems
In the realm of hydraulics, the hydraulic cylinder stands as a pivotal component, effortlessly transforming hydraulic pressure into mechanical force. Picture a piston residing within a cylindrical chamber, meticulously engineered to glide smoothly along its length. When pressurized hydraulic fluid enters the chamber, it exerts an immense force upon the piston, compelling it to extend or retract.
This remarkable interplay between hydraulic pressure and mechanical motion serves as the cornerstone of hydraulic systems, enabling them to perform a myriad of tasks with unparalleled strength and efficiency. From towering cranes hoisting massive loads to precision-engineered medical devices, hydraulic cylinders play an indispensable role in countless applications.
The design of hydraulic cylinders is meticulously crafted to withstand the rigors of high pressure and demanding operating conditions. The piston, meticulously machined to exacting tolerances, ensures a flawless seal against the cylinder walls, preventing fluid leakage and maintaining optimal pressure levels.
To harness the full potential of hydraulic cylinders, they are often paired with other hydraulic components, such as pumps, valves, and reservoirs. This intricate network of components forms a cohesive hydraulic system, seamlessly orchestrated to deliver precise control over force, speed, and motion.
Hydraulic Fluid: The Lifeblood of Hydraulic Systems
Understanding Hydraulic Fluid
In the world of hydraulics, the fluid plays a pivotal role. Hydraulic fluid is the medium through which pressure is transmitted and mechanical force is generated. Its properties are crucial for ensuring the efficient operation of any hydraulic system.
Essential Properties
An ideal hydraulic fluid should possess several key characteristics:
- Incompressibility: Fluids like water tend to compress under pressure, which can lead to inefficiencies. Hydraulic fluid, on the other hand, should be as incompressible as possible to maintain consistent pressure transmission.
- High Viscosity: Viscosity measures the internal resistance of a fluid to flow. A high viscosity prevents excessive leakage and ensures that the fluid can maintain its pressure in the system.
- High Lubricity: Lubricity refers to a fluid's ability to reduce friction between moving parts. Hydraulic fluid acts as a lubricant, protecting components from wear and tear.
- Chemical Stability: High temperatures, pressures, and exposure to various chemicals can deteriorate hydraulic fluid. Chemical stability is essential to ensure that it does not degrade over time.
Functions of Hydraulic Fluid
Beyond its primary function of transmitting pressure, hydraulic fluid serves several other crucial purposes:
- Heat Transfer: Moving hydraulic fluid carries heat away from system components, preventing overheating.
- Corrosion Protection: Some hydraulic fluids contain additives that inhibit corrosion, protecting metal surfaces in the system.
- Power Transmission: By transferring pressure, hydraulic fluid provides the force that drives hydraulic cylinders and other actuators.
Choices and Considerations
Selecting the right hydraulic fluid is key to optimizing system performance. Factors to consider include:
- System Operating Conditions: Temperature, pressure, and environment can affect fluid properties.
- Equipment Compatibility: Different fluids may be specifically designed for certain systems or components.
- Safety and Environmental Concerns: Some fluids may pose hazards to health or the environment.
By understanding the properties and functions of hydraulic fluid, you can ensure that your hydraulic systems operate safely, efficiently, and reliably.
Hydraulic Pressure: An In-Depth Exploration
1. The Basics: Understanding Hydraulic Pressure
Hydraulic pressure is a fundamental concept in engineering, powering a wide range of industrial, construction, and automotive systems. It's the pressure exerted by fluid, typically oil or water, within a closed system. This pressure can be precisely controlled to generate significant force and movement.
2. Components of a Hydraulic System
A hydraulic system consists of several key components, including:
- Hydraulic Cylinder: Converts hydraulic pressure into mechanical force, enabling linear movement or rotation.
- Hydraulic Fluid: Transmits pressure evenly throughout the system, ensuring efficient power transfer.
3. Operation of a Hydraulic System
The operation of a hydraulic system involves a continuous flow of hydraulic fluid through the system. This circuit flow ensures constant pressure throughout the system.
-
Circuit Flow:
The hydraulic fluid is pumped from a reservoir through pipes or hoses to the hydraulic cylinder.- The pipes connect the various components, while the hoses provide flexibility for movement.
-
Pressure Drop:
As the fluid flows through the system, it encounters resistance, resulting in a pressure drop. This pressure loss is due to friction, bends, or blockages in the system. -
Flow Rate:
The flow rate of the fluid determines the speed and force generated by the hydraulic cylinder.- A higher flow rate results in faster movement and greater force.
4. Applications of Hydraulic Pressure
Hydraulic pressure is widely used in a variety of industries, including:
- Industrial machinery: Lifting heavy objects, operating presses, and powering conveyors.
- Construction equipment: Extending booms on cranes, moving earth with excavators, and raising loads.
- Automotive systems: Powering brakes, clutches, and adjustable suspensions.
- Aerospace systems: Controlling flight surfaces, landing gear, and hydraulic pumps.
Pressure Drop: The Hidden Culprit in Hydraulic Systems
In the fascinating world of hydraulics, pressure is the lifeblood that empowers these remarkable systems to deliver immense force and precision control. But as hydraulic fluid journeys through the intricate network of pipes and hoses, it encounters an inevitable force: pressure drop.
Understanding Pressure Drop: The Silent Enemy
Imagine a river flowing gracefully through a winding channel. As the river encounters obstacles like rocks and bends, it loses some of its momentum, resulting in a gradual decrease in its flow rate. Similarly, in a hydraulic system, pressure drop occurs due to friction, turbulence, and other factors that impede the fluid's flow.
Impact on System Performance: A Balancing Act
Pressure drop is a double-edged sword. While some level of pressure loss is inherent in any hydraulic system, excessive pressure drop can significantly impair its performance. This can manifest as:
- Reduced force output from hydraulic cylinders
- Slower operating speeds
- Increased energy consumption as pumps must work harder to maintain pressure
Addressing Pressure Drop: A Delicate Balance
Minimizing pressure drop is a critical design consideration for hydraulic engineers. They employ various strategies to strike a delicate balance, including:
- Selecting pipes and hoses with appropriate diameters and lengths
- Optimizing flow paths to reduce bends and restrictions
- Utilizing components designed to minimize turbulence and friction
- Properly maintaining and cleaning the system to prevent buildup and contamination
Understanding the causes and effects of pressure drop is essential for harnessing the full potential of hydraulic systems. By mitigating pressure loss, engineers can achieve optimal performance, maximize efficiency, and ensure the smooth operation of these remarkable machines.
Flow Rate: Define flow rate and discuss its role in controlling the speed and force of the hydraulic cylinder.
Flow Rate: Controlling the Speed and Force of Hydraulic Cylinders
Hydraulic systems rely on flow rate to precisely control the movement and power of hydraulic cylinders. This critical factor determines the cylinder's speed and force, enabling a wide range of applications.
Understanding Flow Rate
Flow rate measures the volume of hydraulic fluid passing through a component or system per unit of time. Typically expressed in gallons per minute (GPM), flow rate is essential for balancing pressure and velocity within a hydraulic circuit.
Controlling Cylinder Speed
Flow rate directly influences the speed of a hydraulic cylinder. A higher flow rate results in faster movement, as more fluid is supplied to the cylinder. This is particularly important for applications where rapid actuation is required, such as industrial machinery or construction equipment.
Determining Cylinder Force
Flow rate also plays a role in determining the force exerted by a hydraulic cylinder. Higher flow rates allow for greater force, due to the increased volume of fluid pushing against the cylinder's piston. This is crucial for applications where substantial force is needed to move heavy loads or overcome resistance.
Optimizing Flow Rate
Engineers carefully optimize flow rate to achieve the desired performance and efficiency of a hydraulic system. Excessive flow rates can lead to system inefficiencies and increased energy consumption, while insufficient flow rates can starve the cylinder of fluid and hinder its operation.
Applications of Flow Rate Control
Flow rate control enables hydraulic systems to excel in numerous applications. Industrial machinery requires precise motion control and high force for heavy-duty tasks. Construction equipment relies on high flow rates to power hydraulic excavators and cranes. Automotive systems utilize hydraulics for steering, braking, and suspension, demanding responsive flow control. Aerospace systems leverage hydraulics for flight control systems, where accurate and reliable flow regulation is critical.
Describe various industries where hydraulic pressure is utilized, such as:
- Industrial machinery
- Construction equipment
- Automotive systems
- Aerospace systems
Industrial Machinery:
Hydraulic pressure is a crucial component in powering and controlling industrial machinery, from massive cranes and excavators to automated assembly lines. Its ability to generate tremendous force with precise control allows for efficient handling and manipulation of heavy loads, ensuring safety and productivity in demanding industrial settings.
Construction Equipment:
Hydraulic pressure plays a vital role in the operation of construction equipment, such as bulldozers, excavators, and backhoes. It provides the immense force needed to lift and move massive amounts of earth and materials. The precise hydraulic controls enable operators to perform intricate maneuvers with ease, enhancing productivity and reducing strain on workers.
Automotive Systems:
Hydraulic pressure is essential in various automotive applications, including power steering, braking, and suspension systems. In power steering, hydraulic pressure assists in turning the steering wheel, making it effortless to navigate even heavy vehicles. In braking systems, it amplifies the force applied to the brake pedal, ensuring prompt and controlled stopping.
Aerospace Systems:
Hydraulic pressure is used extensively in aerospace systems, where it powers and controls critical functions such as landing gear, flight controls, and hydraulic systems. Its high power-to-weight ratio and reliability make it an ideal solution for the demanding conditions encountered in aviation. Hydraulic systems provide the precise and reliable force needed for maneuvering aircraft, ensuring flight safety and efficiency.
Industrial machinery
Understanding Hydraulic Pressure in Industrial Machinery
In the realm of industrial machinery, hydraulic pressure plays a vital role in converting force into motion. It's a fundamental principle that governs the operation of countless machines, from heavy-duty excavators to precision stamping presses.
Pascal's Law: The Cornerstone of Hydraulics
The foundation of hydraulics lies in Pascal's Law. This law states that pressure applied to a fluid is transmitted equally to every point within the fluid. It's a simple yet powerful principle that enables hydraulic systems to generate immense forces with relatively small inputs.
Hydraulic Pressure: The Force Multiplier
Hydraulic pressure is measured in units of force per unit area (typically pounds per square inch, or psi). It's a measure of the force exerted by the hydraulic fluid on the surfaces it contacts. By applying pressure to a confined volume of fluid, we can amplify the applied force, resulting in a greater output force.
Components of a Hydraulic System
A hydraulic system consists of several essential components:
- Hydraulic Cylinder: This cylindrical device converts hydraulic pressure into mechanical force. It contains a piston that moves within a cylinder bore, generating linear motion.
- Hydraulic Fluid: The lifeblood of a hydraulic system, this fluid transmits pressure and lubricates components. It must possess specific properties, such as resistance to wear and high viscosity.
Operation of a Hydraulic System
The operation of a hydraulic system involves several key steps:
- Circuit Flow: Hydraulic fluid flows through the system in a continuous loop, powered by a pump.
- Pressure Drop: As the fluid flows through pipes and hoses, it encounters resistance, causing a gradual pressure drop.
- Flow Rate: The rate at which the fluid flows through the system affects the speed and force of the hydraulic cylinder.
Applications in Industrial Machinery
Hydraulic pressure finds myriad applications in industrial machinery, including:
- Machine Tools: Hydraulic systems power cutting and shaping tools, providing precise control and high force generation.
- Material Handling: Hydraulic cylinders lift, move, and position heavy loads with ease.
- Construction Equipment: Excavators, cranes, and other construction machinery rely on hydraulics for power and versatility.
- Automotive Systems: Hydraulic systems are used in power steering, braking, and transmission systems, improving vehicle performance and safety.
- Aerospace Systems: Hydraulics play a crucial role in aircraft flight controls, landing gear, and braking systems.
By harnessing the power of hydraulic pressure, industrial machinery can achieve extraordinary levels of force, precision, and efficiency. From heavy-duty excavations to delicate surgical procedures, hydraulic systems continue to revolutionize the way we interact with the world around us.
Hydraulic Pressure in Construction Equipment: A Forceful Ally
In the rugged world of construction, hydraulic pressure stands as a mighty force, powering heavy machinery and enabling them to perform extraordinary feats. Understanding the principles behind hydraulic pressure is crucial for appreciating its transformative impact on construction operations.
The Strength of Hydraulic Pressure
Hydraulic pressure harness the fundamental principle of Pascal's Law, which states that pressure applied to a fluid is transmitted uniformly throughout. This means that when pressure is applied to a hydraulic fluid, it exerts equal force on every surface within the system.
In construction equipment, hydraulic pressure is created by a hydraulic pump, which pressurizes the hydraulic fluid and directs it through a network of pipes and hoses to hydraulic cylinders. These cylinders convert the hydraulic pressure into mechanical force, allowing for precise control over the movement of equipment components.
The Heart of a Hydraulic System: Hydraulic Fluid
The secret ingredient that powers hydraulic systems is the hydraulic fluid. This fluid is specially formulated to withstand high pressures and temperatures, ensuring reliable and consistent performance. Its primary role is to transmit pressure from the pump to the hydraulic cylinders. Additionally, hydraulic fluid also acts as a lubricant, preventing wear and tear on system components.
Inside the Hydraulic Circuit
The movement of hydraulic fluid through the system is known as hydraulic circuit flow. This flow begins at the hydraulic pump, where the fluid is pressurized. It then travels through pipes and hoses to the hydraulic cylinders, where it exerts force to extend or retract the cylinder's piston. As the fluid returns to the pump, it may encounter pressure drop, which is a gradual loss of pressure due to friction and other factors.
Control and Performance: Flow Rate and Pressure Drop
Flow rate is a critical factor in determining the speed and force of hydraulic cylinders. A higher flow rate allows for faster movement and greater force, while a lower flow rate results in slower movement and reduced force.
Pressure drop also plays a significant role in system performance. Excessive pressure drop can lead to underperformance and potential damage to equipment components. Therefore, hydraulic systems are designed to minimize pressure drop through proper sizing of pipes and hoses, and by using efficient pump and valve components.
Hydraulic Pressure at Work in Construction
Hydraulic pressure is an indispensable tool in a wide range of construction equipment, including:
- Excavators: Hydraulic pressure powers the powerful arm and bucket, allowing for precise digging and lifting.
- Cranes: Hydraulic cylinders enable cranes to lift and move heavy loads with ease.
- Bulldozers: Hydraulic pressure drives the massive blades, enabling them to push and level soil and other materials.
- Concrete mixers: Hydraulic motors power the mixer drum, ensuring thorough mixing of concrete.
Hydraulic pressure has revolutionized construction by providing a compact and efficient means of generating and transmitting force. Its ability to control movement, speed, and force makes it the ideal power source for the demanding tasks encountered in construction.
Automotive systems
Understanding Hydraulic Pressure
Introduction:
In the realm of engineering, hydraulic pressure plays a pivotal role in harnessing the power of fluids to perform intricate tasks. It's a fundamental concept that has revolutionized the way we design and operate machinery, from industrial giants to the vehicles we drive every day.
1. Pascal's Law: The Foundation of Fluid Pressure
At the heart of hydraulic pressure lies Pascal's Law, which states that pressure applied to a fluid is transmitted equally to all points within the fluid. In simpler terms, when you push on a fluid, the force you exert is distributed evenly throughout the liquid or gas.
2. Hydraulic Pressure: Force, Area, and Power
Hydraulic pressure is the force per unit area exerted by a fluid. It's directly proportional to the applied force and inversely proportional to the surface area over which the force is applied. This relationship empowers engineers to design systems that can generate immense power with relatively small forces.
Components of a Hydraulic System
3. Hydraulic Cylinder: Muscle of the System
The hydraulic cylinder is the mechanical heart of a hydraulic system. It converts hydraulic pressure into linear force. When hydraulic fluid flows into the cylinder, it exerts pressure on a piston, which in turn pushes a rod outwards. This linear motion is used to operate a wide range of machinery.
4. Hydraulic Fluid: The Messenger of Power
Hydraulic fluid is the lifeblood of any hydraulic system. It transmits pressure and lubricates moving parts. Its properties, such as viscosity and temperature stability, are crucial for the efficient operation of the system.
Operation of a Hydraulic System
5. Circuit Flow: Tracing the Fluid's Journey
In a hydraulic circuit, the fluid travels along a path defined by pipes and hoses. The fluid enters the system through a pump, which increases its pressure. It then flows through valves, which control the direction and flow rate, before reaching the hydraulic cylinder.
6. Pressure Drop: The Resistance Faced by Fluid Flow
As hydraulic fluid travels through the system, it encounters resistance due to friction and other factors. This resistance results in a pressure drop, which must be considered when designing and operating the system.
7. Flow Rate: Controlling Speed and Force
Flow rate measures the volume of fluid passing through a given point in a unit of time. By controlling the flow rate, engineers can adjust the speed and force generated by the hydraulic cylinder.
Applications of Hydraulic Pressure
8. Automotive Systems: Powering Vehicles
In the automotive industry, hydraulic pressure plays a crucial role in:
- Braking systems: Hydraulic brakes utilize fluid pressure to distribute braking force evenly and effectively to all four wheels.
- Power steering: Hydraulic power steering systems provide assisted steering, making it easier to maneuver vehicles.
- Suspension systems: Hydraulic suspension systems enhance ride comfort and stability by controlling the movement of the suspension components.
Hydraulic pressure is an indispensable tool in modern engineering, empowering us to create systems that perform complex tasks with precision and efficiency. From industrial machinery to automotive systems, its applications are vast and transformative. Understanding the principles of hydraulic pressure lays the foundation for designing and operating these systems to their full potential.
Hydraulic Pressure: A Vital Force in Aerospace Systems
In the vast expanse of the cosmos, where cutting-edge technology reigns supreme, hydraulic pressure plays a pivotal role in propelling and controlling aircraft. Join us as we delve into this fascinating realm, unraveling the intricacies of hydraulic systems and their indispensable contribution to the wonders of flight.
Understanding the Fundamentals
Hydraulic pressure, as described by Pascal's Law, is a force exerted by a fluid (liquid) enclosed in a confined space that acts equally in all directions. When force is applied to the fluid, it transmits this pressure uniformly throughout the system. In hydraulic systems, this pressure is harnessed to perform a wide range of functions.
Components of a Hydraulic System
At the heart of a hydraulic system lies the hydraulic cylinder. This device converts hydraulic pressure into mechanical force, enabling the effortless movement of aircraft components such as flaps, ailerons, and landing gear. Hydraulic fluid, the lifeblood of the system, plays a crucial role in transmitting pressure efficiently while also lubricating and cooling moving parts.
Operation: A Symphony of Fluid Dynamics
Fluid flows through the system's circuit, a network of pipes and hoses connecting its various components. As the fluid circulates, pressure drop occurs due to friction and resistance in the circuit. Understanding this pressure loss is essential for optimizing system performance. Flow rate, governed by valves and pumps, determines the speed and force with which the hydraulic cylinder operates.
Applications: Powering Innovation in the Skies
The realm of aerospace presents a multitude of applications for hydraulic pressure. In industrial machinery, hydraulics empowers heavy-duty equipment used in manufacturing and construction. It drives the mighty cranes that lift towering structures and the bulldozers that shape the landscape. In automotive systems, hydraulics enhance braking performance, power steering, and transmission.
But it is in aerospace systems where hydraulic pressure truly takes flight. From the hydraulic flight controls that guide aircraft with precision to the landing gear that safely supports their weight, hydraulics empowers every aspect of aviation. In the vastness of space, where reliability and efficiency are paramount, hydraulic pressure stands as an unsung hero, ensuring the smooth operation and safety of our celestial journeys.
Related Topics:
- Comprehensive Guide To Fossil Types: Body Fossils, Trace Fossils, Chemical Fossils, And More
- Maximize Argon Gas Pricing Strategy: Key Factors To Consider
- Unveiling The Multifaceted Word “Relief”: A Linguistic Exploration For Seo Proficiency
- Elephant Toothpaste: Unlocking The Secrets Of A Thrilling Decomposition Reaction
- Men’s Guide To Respecting Women: Equality, Consent, And More